Underwater production systems typically rely on their own pressure for extraction. For some few underwater production systems, it is necessary to use water/gas injection or underwater booster pumps to maintain system pressure. Developing certain underwater production systems with deep water depth, heavy heavy oil, small reservoir reserves, unknown reserves or low recovery rates, low/extremely high fluid pressure, flow guarantee requirements, long return distance, and mature use of Phase I booster pumps can consider using underwater booster pumps placed on the seabed for development. The use of underwater booster pumps for oil and gas development can effectively increase oil recovery, promote production, and simplify infrastructure such as upper platforms.
The Application of Underwater Booster Pump in Underwater Production System
The underwater production system of a certain oilfield includes three underwater Christmas trees, with a water depth of about 500 meters. The oil and gas production is connected back to an upper offshore platform. The use of an underwater production system development plan and the use of an underwater booster pump lifting oil extraction method can achieve high-speed and efficient development of the oil field and improve oil recovery. The geological reservoir characteristics of a certain oilfield indicate that sandstone reservoirs have good physical properties, high production capacity, and abundant formation energy. The formation energy is used to lift the fluid to the seabed, and then a booster pump is used for production.
Overall requirements for underwater booster pumps:
The underwater booster pump system includes an integrated underwater booster pump module on the underwater manifold, and the related power and control equipment of the booster pump arranged on the upper platform, including MCS, EPU, VFD, HPU, BPU (isolation fluid unit), etc. And the components related to the booster pump in the umbilical cable, as well as the special tools for operating, installing, and recycling the booster pump.
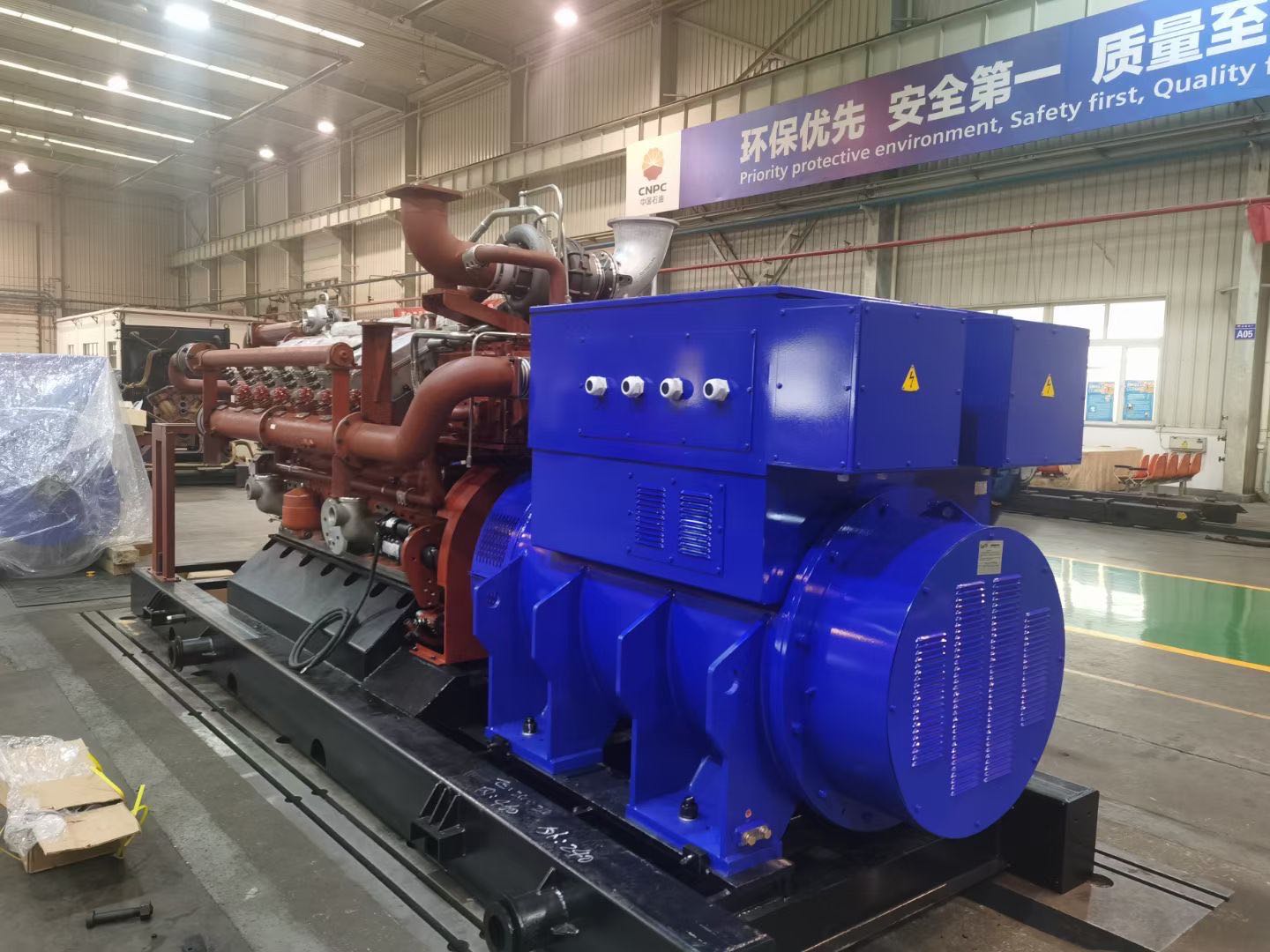
The underwater booster pump module is integrated on the underwater manifold, and is designed as a recyclable form that can be lifted to the surface for maintenance, and connected and disengaged using ROV. The underwater booster pump should be designed to adapt to water depth. According to the current production allocations and operating conditions of a certain oil field, gas will not appear during the transportation process of the booster pump, and the underwater booster pump adopts a single-phase pump. The range of GVF (gas volume fraction) that single-phase pumps can adapt to is 0-10%.
In terms of underwater booster pump maintenance, it is necessary to understand the underwater maintenance space, installation and repair tools, and other requirements of the booster pump, which will be reflected in the design.
Design of underwater booster pump module:
The size of the booster pump module in a certain oilfield is about 4mX3.5mX6m, and the weight is about 50 tons. The entire underwater booster pump module includes the module structure of the ROV operation panel, including the pump body, gearbox, pump process pipeline interface, control interface/isolation liquid interface/HIGH VOLTAGE interface.
The underwater booster pump adopts a vertical pump, with the pump shaft and motor installed vertically, and the motor box located above the pump body. The motor is equipped with VFD on the upper module to meet various operating conditions within the design life of the underwater booster pump.
The process inlet and outlet pipeline interface of the underwater booster pump is located directly below the pump body. The inlet and outlet pipelines of the booster pump use underwater vertical connectors to quickly and accurately connect with the pipeline interface on the manifold, while facilitating the disconnection from the pipeline on the manifold when lifting the underwater booster pump.
The ROV operation panels of the underwater booster pump are all set on the same side to facilitate underwater connection and operation of the ROV. The operation panel includes interfaces such as control electric flying wires, hydraulic flying wires (including hydraulic/chemical agents), isolation liquid flying wires, and HIGH VOLTAGE flying wires.
The manifold protection cover on one side of the ROV operation panel of the underwater booster pump is designed to be open, while the other three sides can be designed to be protected with protective covers to greatly protect the internal facilities and pump body of the manifold. The booster pump should be equipped with an ROV operating handle, and the ROV operating panel should be convenient for ROV connection and operation. It should be located above the 1.5 meter mud line and need to consider the ROV operating space.
The top of the underwater booster pump is equipped with lifting eyes. Due to the need for lifting during maintenance of the underwater booster pump, a top door should be installed on the protective cover of the manifold above the pump body to achieve the function of lifting and protecting the pump body. The underwater booster pump module is equipped with a guide rod.